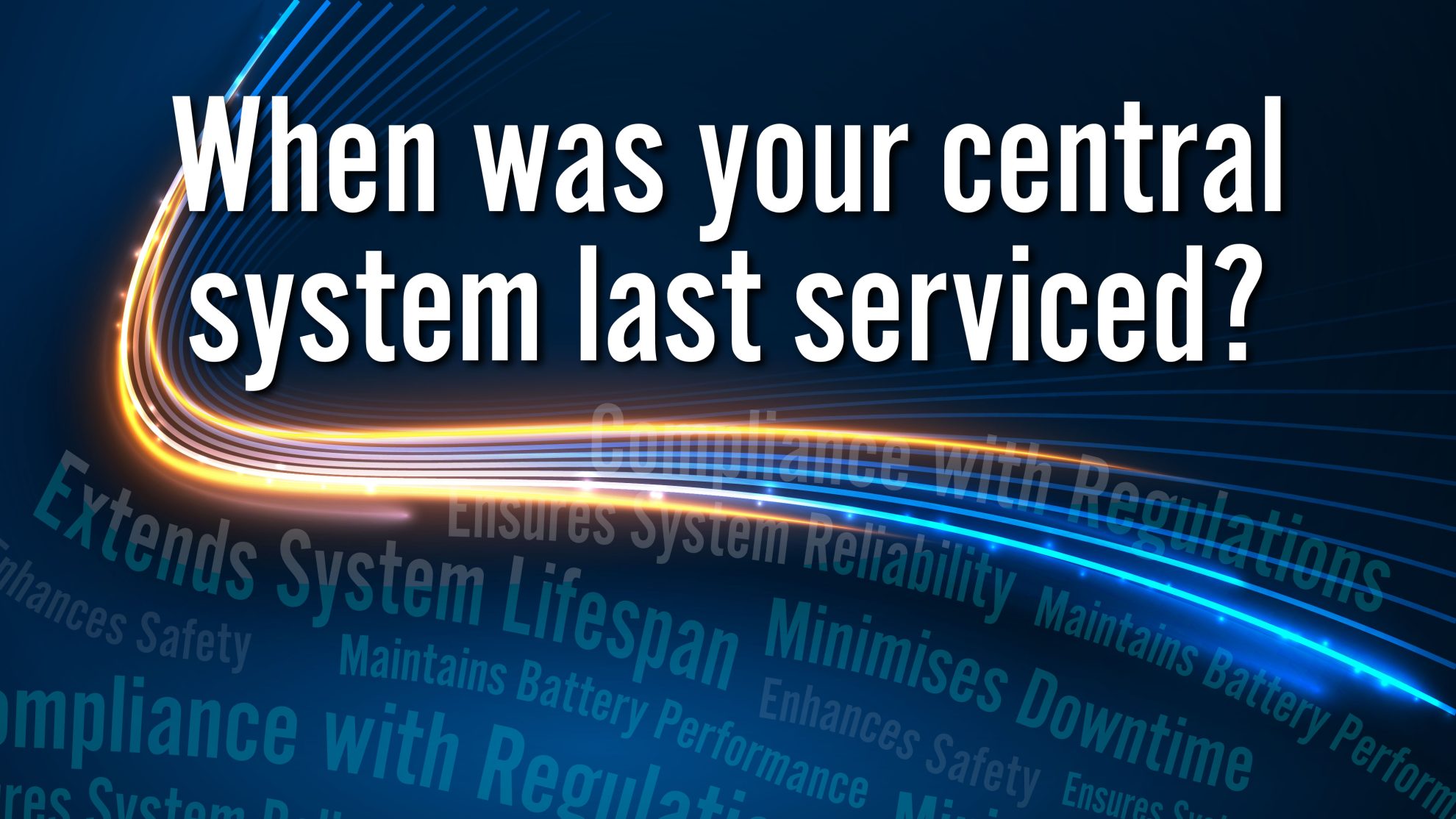
Regular maintenance of a central battery emergency lighting system is critical for ensuring its reliability, compliance, and performance when it matters most.
1. Ensures System Reliability
-
A central battery system powers multiple emergency luminaires from a single source. If this system fails, it can jeopardise the entire emergency lighting network. Regular maintenance identifies and resolves potential faults before they escalate, ensuring the system is always operational.
2. Compliance with Regulations
- Maintenance is required to meet legal standards such as BS 5266-1 and BS EN 50171, which mandate regular checks to ensure emergency lighting systems are fit for purpose. Proper documentation of testing and maintenance is also essential for compliance audits.
3. Extends System Lifespan
- Regular inspections and servicing help prevent wear and tear, prolonging the life of batteries, control equipment, and other components. This reduces the need for costly replacements and downtime.
4. Maintains Battery Performance
- Central batteries, often the heart of the system, degrade over time. Routine maintenance ensures batteries are adequately charged, free from corrosion, and replaced when nearing the end of their service life (typically 10 years for sealed lead-acid batteries).
5. Minimises Downtime
- Identifying and fixing faults during scheduled maintenance reduces the likelihood of unexpected failures during an emergency, ensuring continuous operation.
6. Enhances Safety
- The primary purpose of an emergency lighting system is to provide illumination for safe evacuation during a power failure. Regular maintenance ensures the system performs as designed, protecting lives during emergencies.
7. Reduces Liability Risks
- A poorly maintained system can lead to non-compliance and increased liability if it fails during an emergency. Regular checks demonstrate a proactive approach to safety and compliance, reducing legal risks.
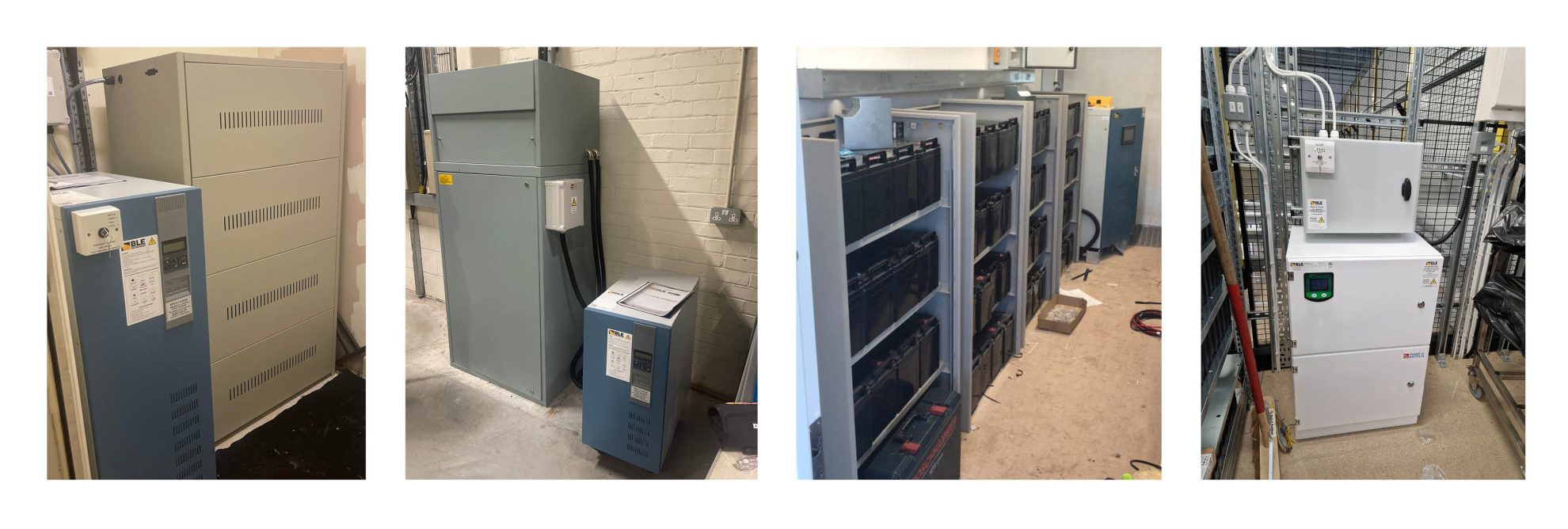